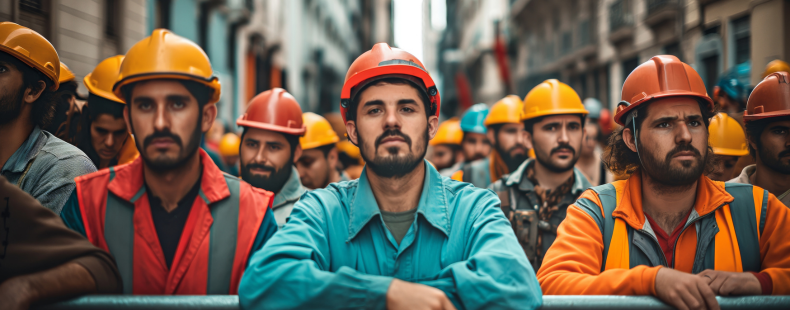
LearnTastic’s OSHA 10 certification empowers construction workers and contracto...
Read More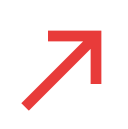
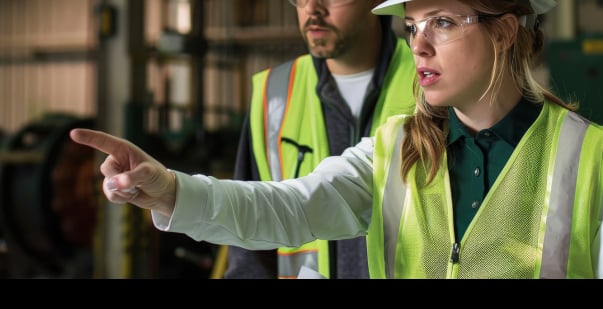
Discover how OSHA 10 training transforms construction from a high-risk zone to a...
Read More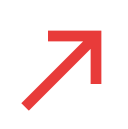
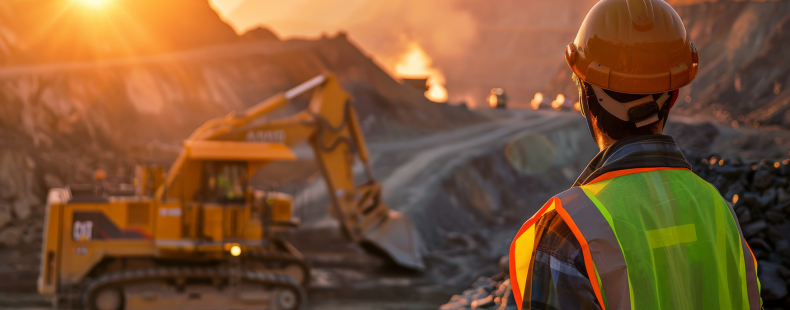
LearnTastic’s OSHA 10 training can help you stand out as a safety-first partner...
Read More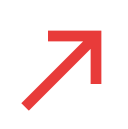
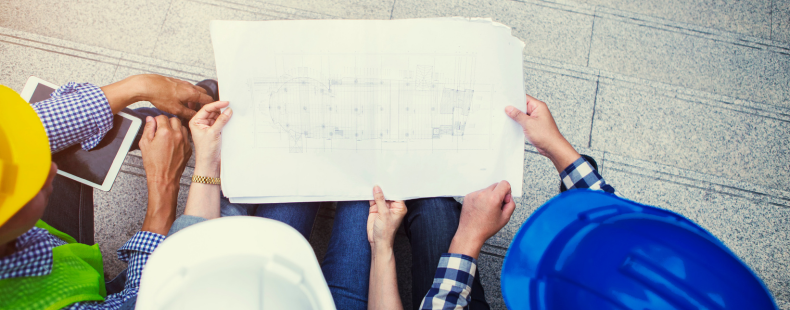
Unpack the process of obtaining your OSHA 10 certification, a crucial step towar...
Read More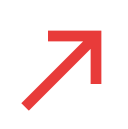
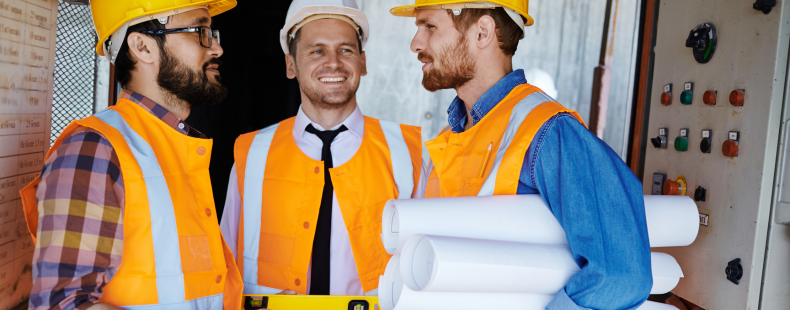
Explore LearnTastic’s OSHA 10 Construction Course & empower your workforce with...
Read More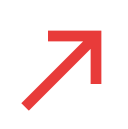
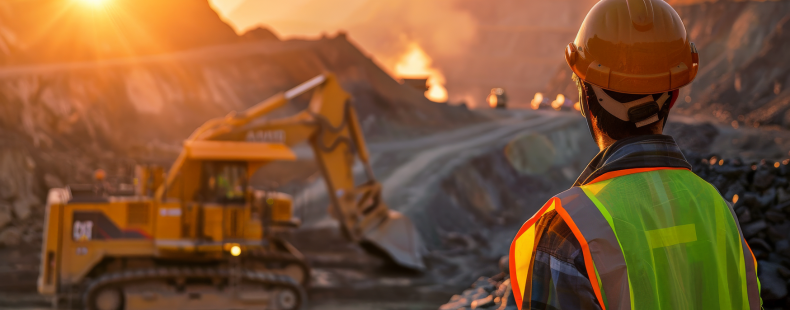
OSHA 10 vs. OSHA 30: Understand the key differences between basic safety trainin...
Read More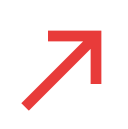
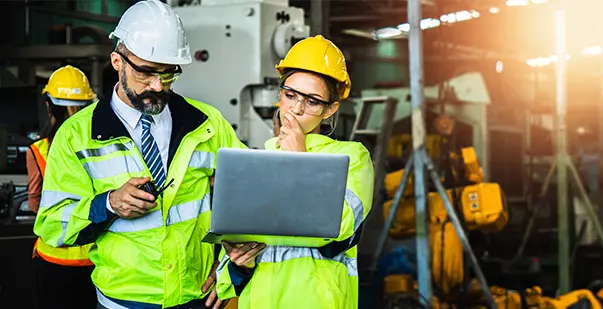
Understanding OSHA standards is crucial for workplace safety. Key standards incl...
Read More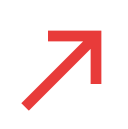
.webp)
OSHA certification ensures workers are trained in safety standards, hazard recog...
Read More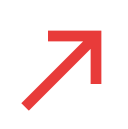
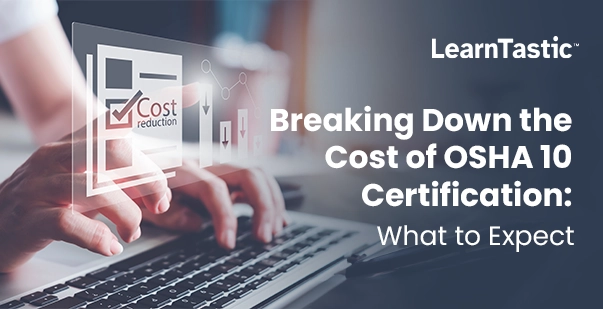
Curious about OSHA 10 certification costs? We break down the expenses, covering...
Read More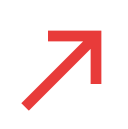
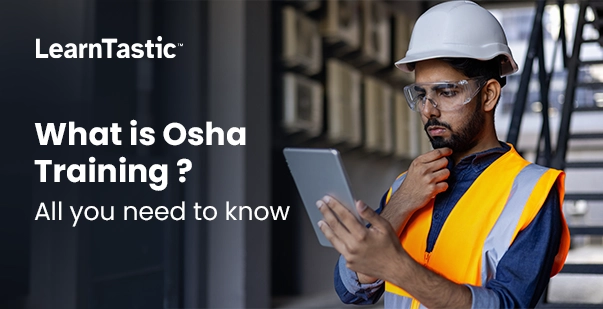
OSHA training equips workers with the knowledge to recognize and avoid workplace...
Read More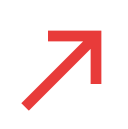
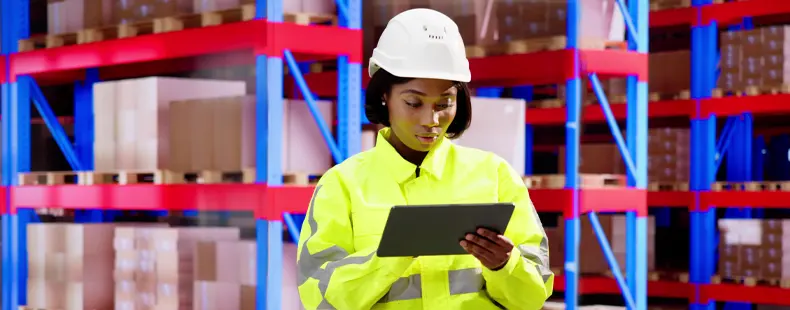
Wondering how to maintain and renew your OSHA certification? Stay compliant by u...
Read More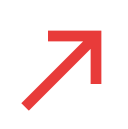
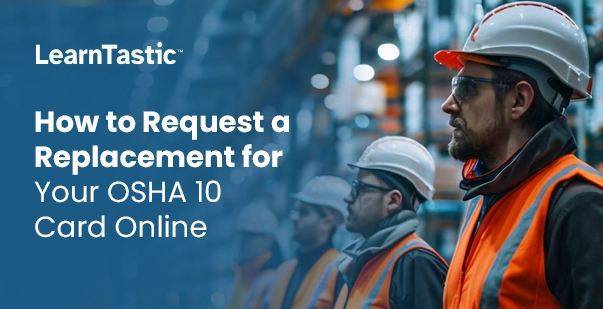
Lost your OSHA 10 card? Don’t worry! Requesting a replacement online is easy. Fo...
Read More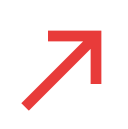
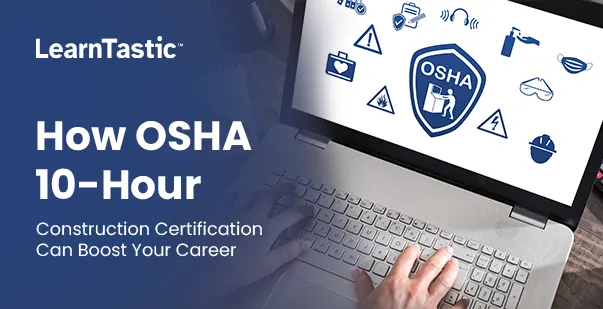
Earning an OSHA 10-Hour Construction Certification enhances your safety knowledg...
Read More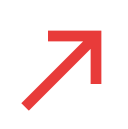
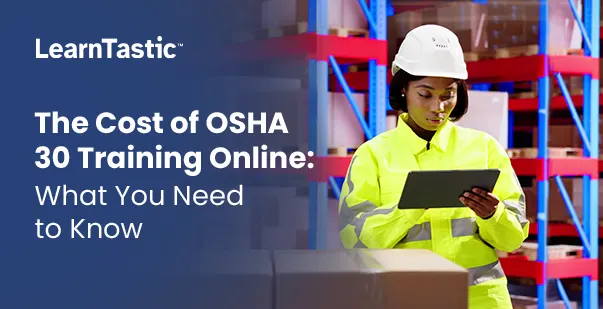
The cost of OSHA 30 training online varies, typically ranging from $150 to $300....
Read More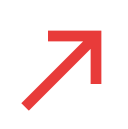
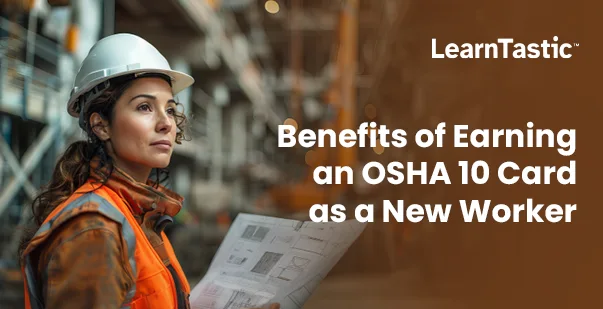
Earning an OSHA 10 card as a new worker enhances safety knowledge, reduces workp...
Read More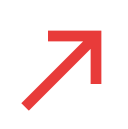
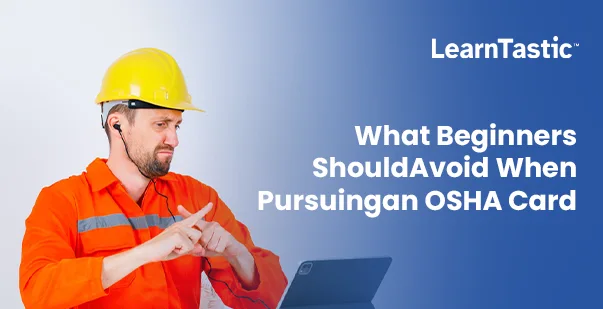
Beginners should avoid skipping proper study, choosing uncertified providers, an...
Read More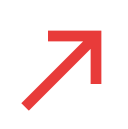
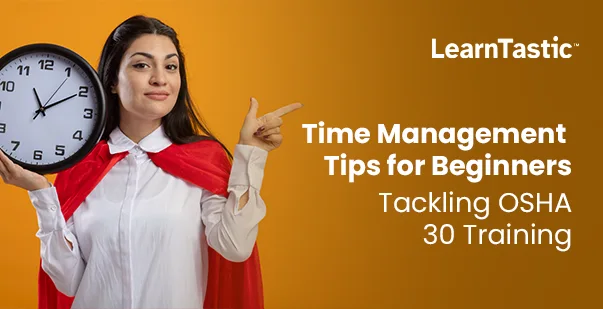
Struggling to balance your OSHA 30 training with daily tasks? Start small—break...
Read More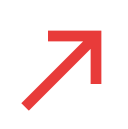
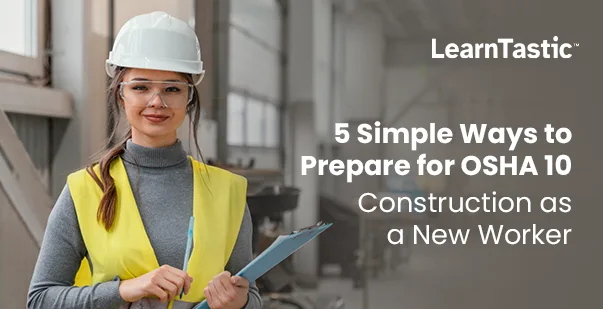
New to OSHA 10 Construction? Start strong by reviewing course materials, taking...
Read More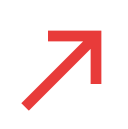
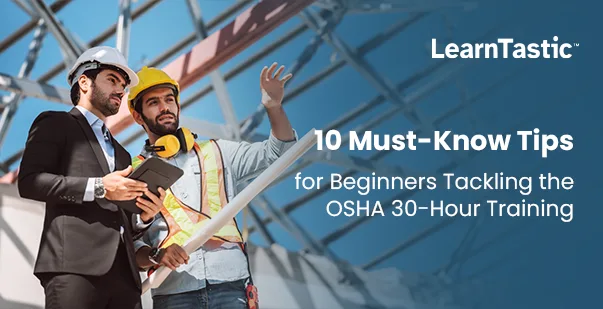
New to OSHA 30-Hour training? Break it down! From setting a study schedule to us...
Read More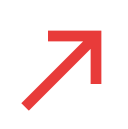
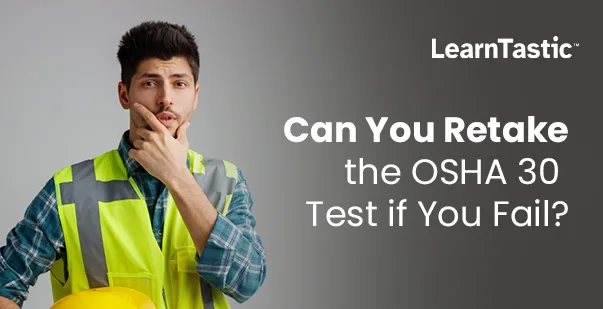
If you fail the OSHA 30 test, don't worry! You can retake it. Most courses allow...
Read More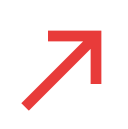
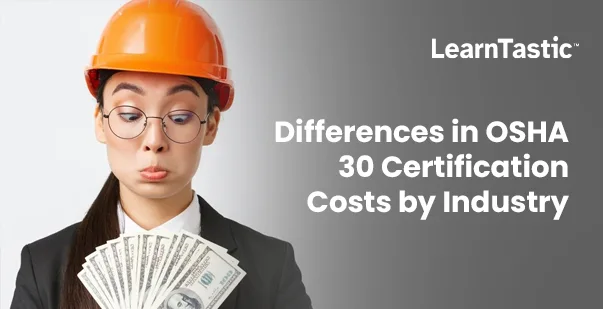
OSHA 30 certification costs vary by industry, with construction and general indu...
Read More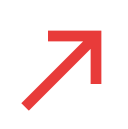
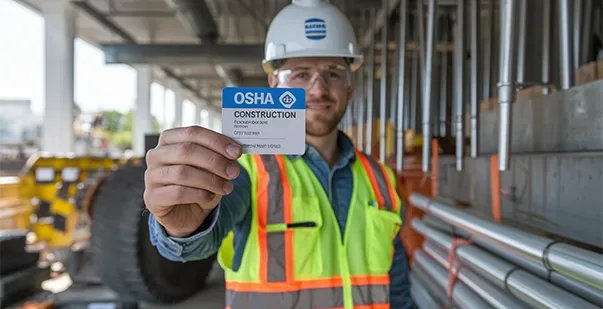
Uncover the truth behind common myths about OSHA 10-Hour Construction Certificat...
Read More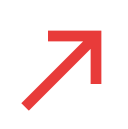
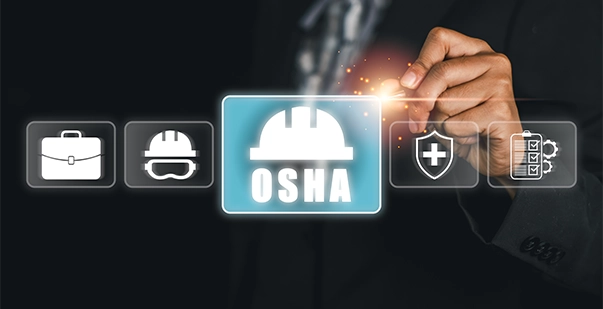
If you've lost your OSHA 10 card, you can request a replacement by providing key...
Read More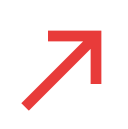
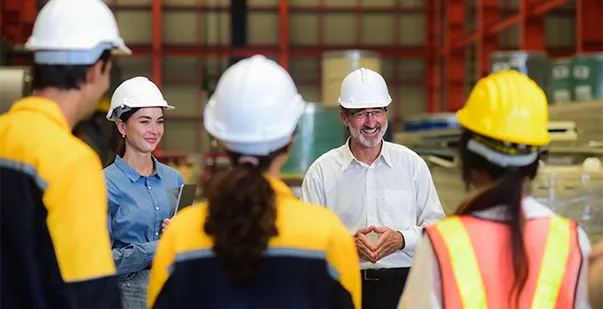
OSHA 40-hour training offers vital benefits, including enhanced workplace safety...
Read More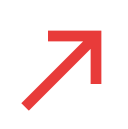
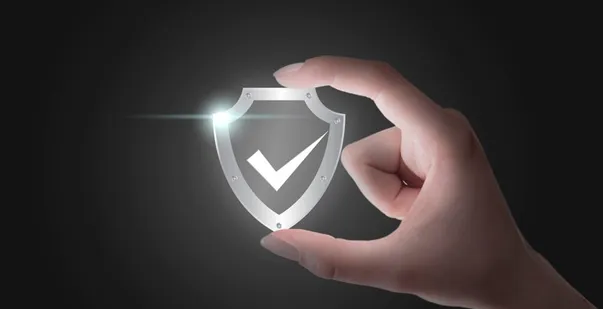
Fall protection training educates workers on preventing falls at heights, proper...
Read More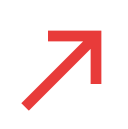
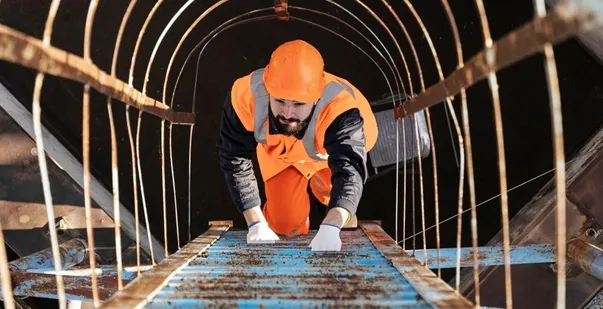
OSHA Confined Space Training equips workers with the skills to identify hazards,...
Read More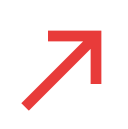
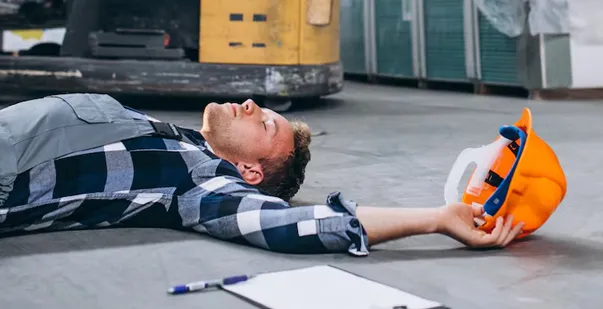
OSHA violations include lack of fall protection, improper hazard communication,...
Read More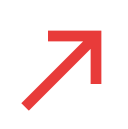
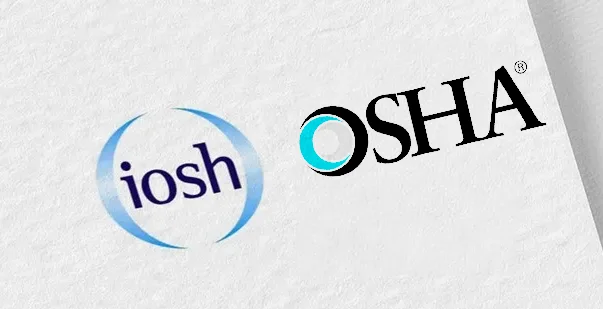
Choosing between IOSH and OSHA? IOSH focuses on workplace safety in the UK, whil...
Read More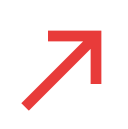
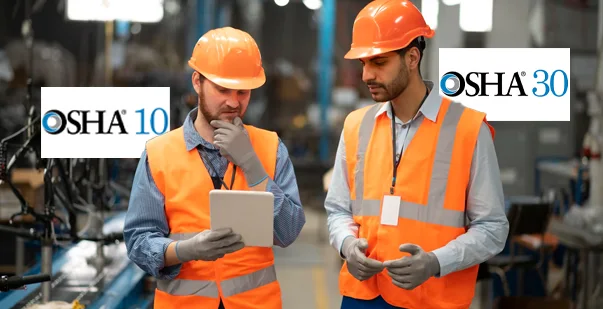
Wondering if OSHA 30 is better than OSHA 10? It depends on your role! OSHA 30 of...
Read More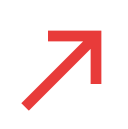
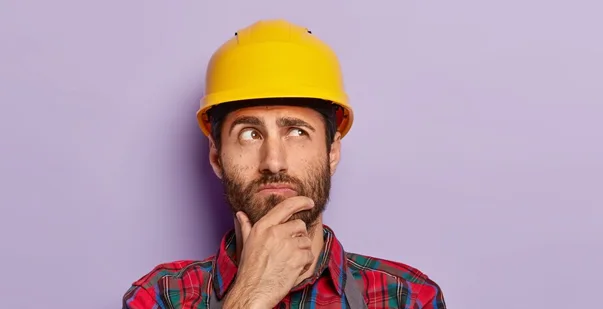
Wondering how tough OSHA certification is? It’s more about focus than difficulty...
Read More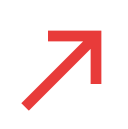
.webp)
Wondering how long your OSHA 30 certification stays valid? OSHA 30 cards don’t e...
Read More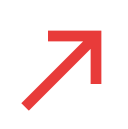
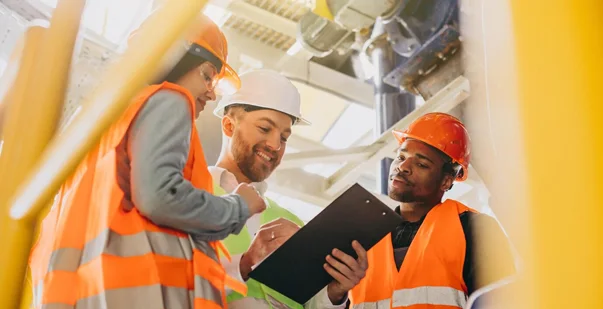
Learn about the validity of OSHA 10 certification, its renewal requirements, and...
Read More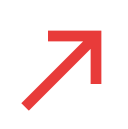
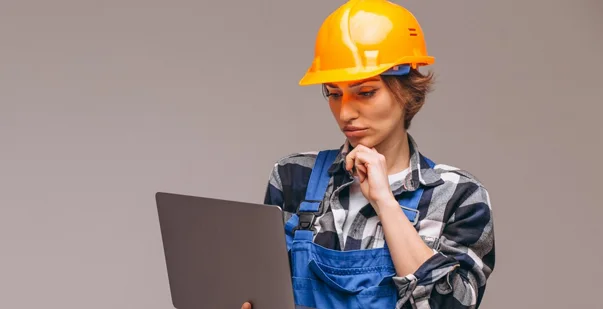
Discover the essentials of workplace safety with OSHA 10-hour training. Learn ha...
Read More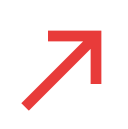
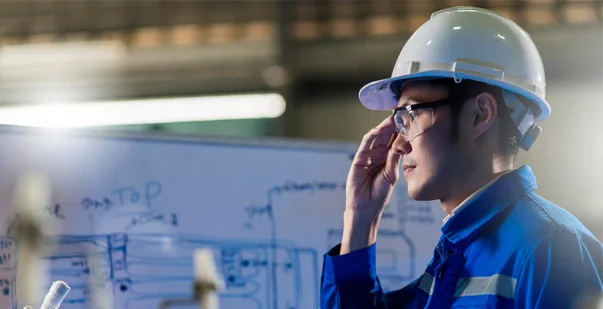
Wondering if OSHA 10 online certifications are accepted by employers? Discover h...
Read More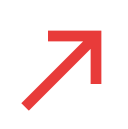
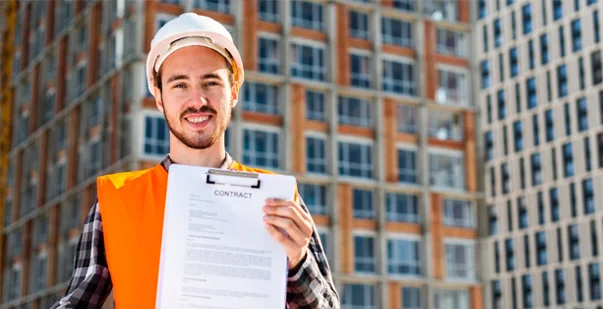
Explore the key differences between in-person and online OSHA 10 certification,...
Read More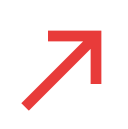
.webp)
Prepare for success with the OSHA 10 Practice Test! Boost your workplace safety...
Read More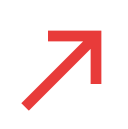
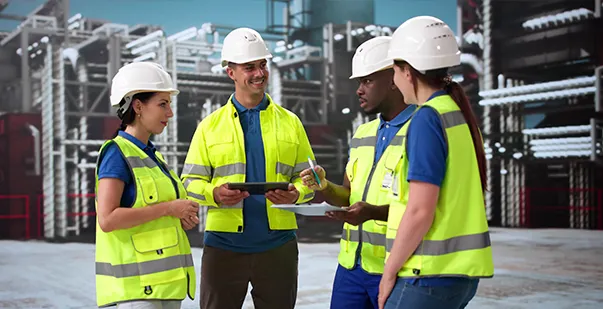
An Emergency Action Plan (EAP) is a structured guide outlining steps to handle w...
Read More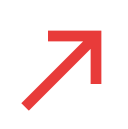
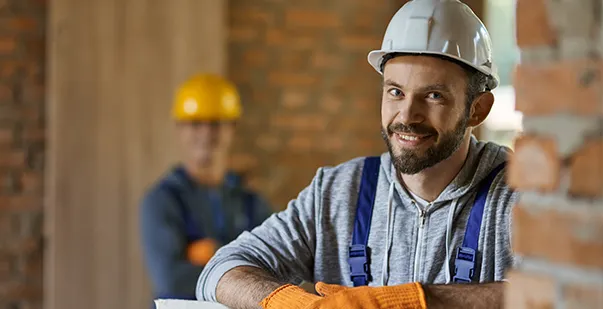
Dreaming of a career in construction? Learn the step-by-step process to become a...
Read More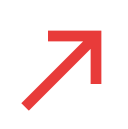
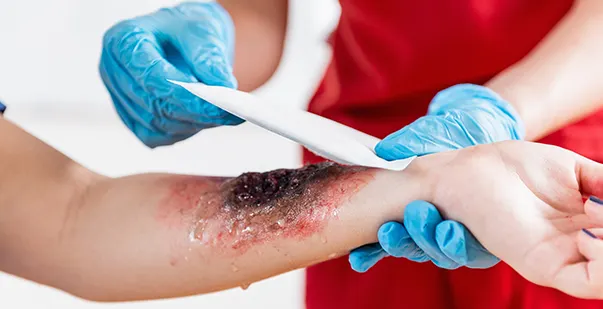
Concrete burns can cause severe skin damage if not treated promptly. Learn the e...
Read More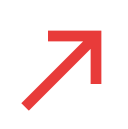
.webp)
Electrical hazards in the workplace include shocks, burns, electrocution, and fi...
Read More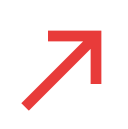
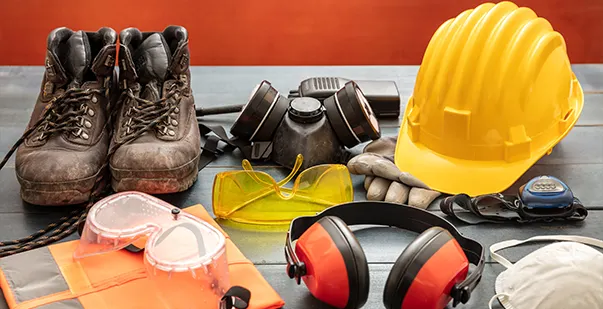
Personal Protective Equipment (PPE) includes gear like gloves, masks, and helmet...
Read More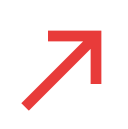
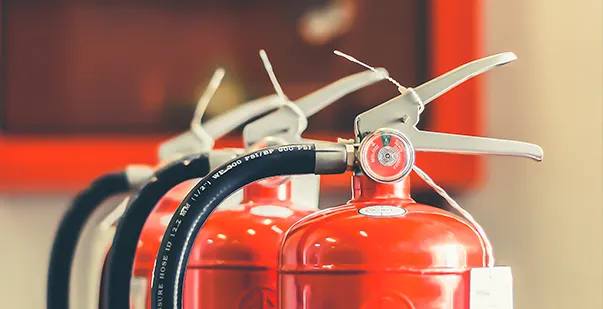
Quickly control fires with PASS: Pull the pin, Aim at the base, Squeeze the hand...
Read More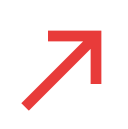
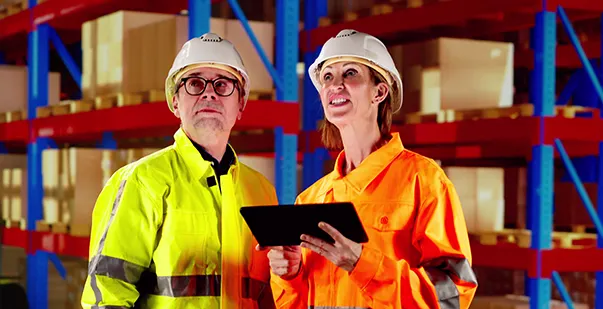
OSHA's General Duty Clause requires employers to provide a workplace free from r...
Read More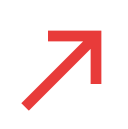
.webp)
Losing an hour of sleep? It’s not just grogginess—Daylight Saving Time increases...
Read More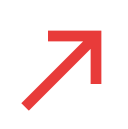
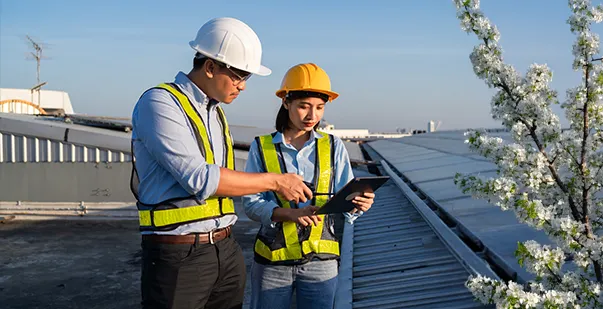
As construction ramps up this spring, OSHA is tightening safety regulations. Fro...
Read More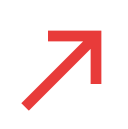
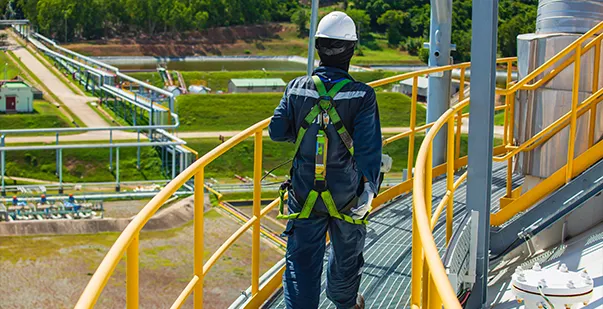
OSHA handrail requirements ensure workplace safety by setting standards for heig...
Read More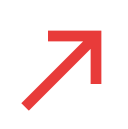
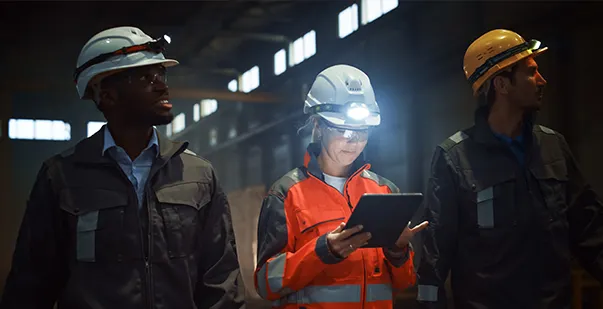
Get the scoop on MSHA certification! Learn what it is, who needs it, and how min...
Read More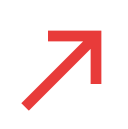
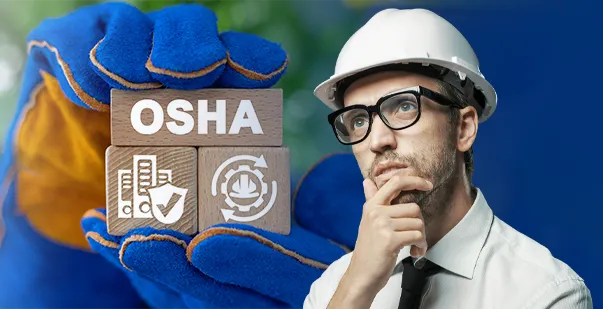
Discover how OSHA enforces workplace safety—learn about inspections, citations,...
Read More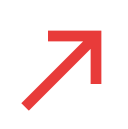
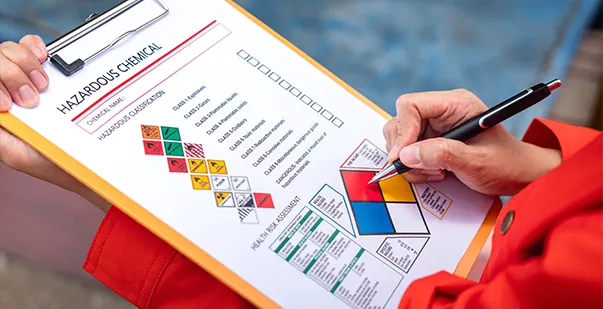
Ace your Hazmat certification with expert prepation tips and sample questions! T...
Read More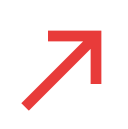
.webp)
Asphyxiation in confined spaces occurs when there's not enough oxygen or toxic g...
Read More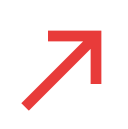
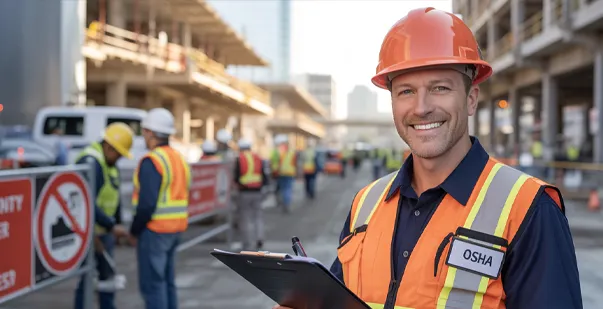
An OSHA inspector ensures workplaces follow safety regulations, helping prevent...
Read More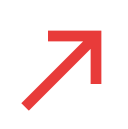
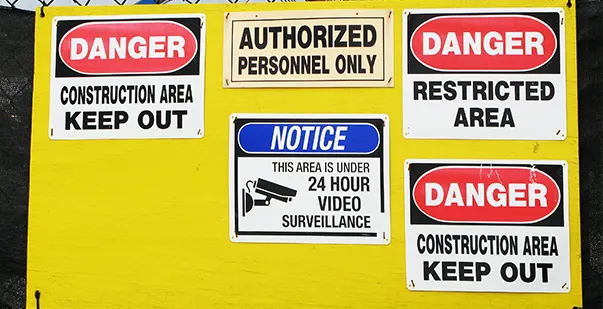
Stay compliant and keep your workplace safe! Learn all about OSHA sign requireme...
Read More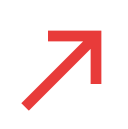
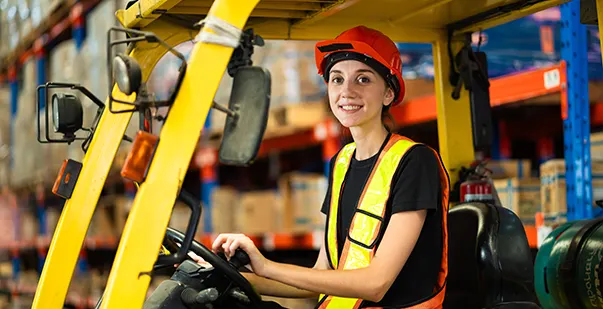
Wondering how old you need to be to drive a forklift? Learn the legal age requir...
Read More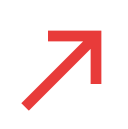
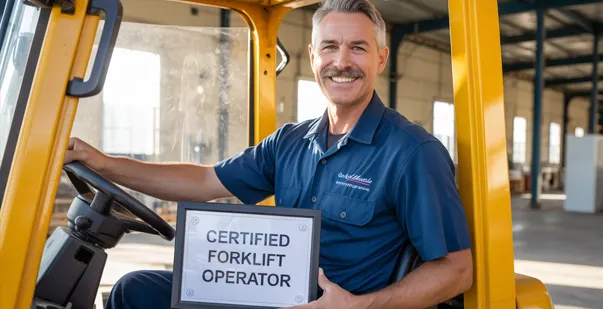
Looking to get forklift certified? Discover the best places—online and in-person...
Read More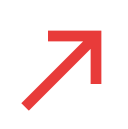
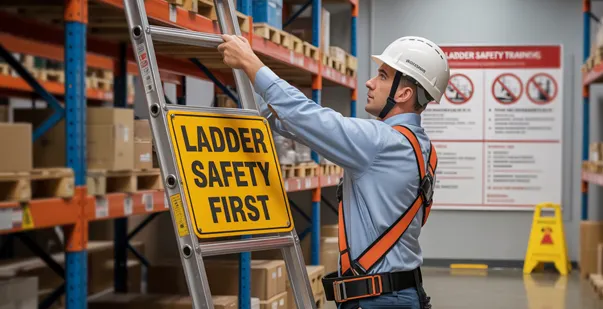
OSHA Ladder Safety Training teaches workers how to properly use ladders on the j...
Read More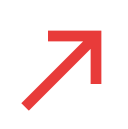
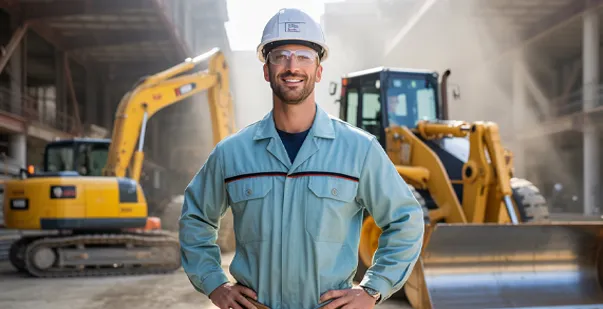
Heavy equipment operators handle powerful machines like bulldozers and excavator...
Read More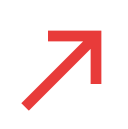
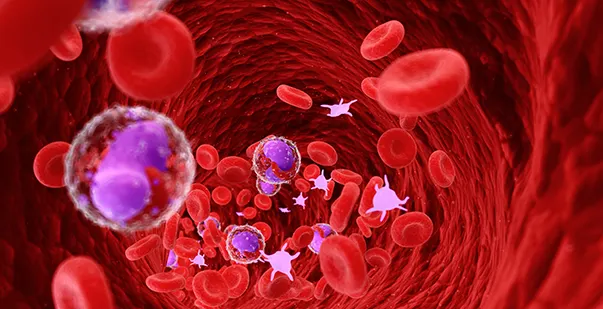
Discover what the OSHA Bloodborne Pathogens Standard is, who it protects, and ho...
Read More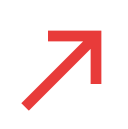
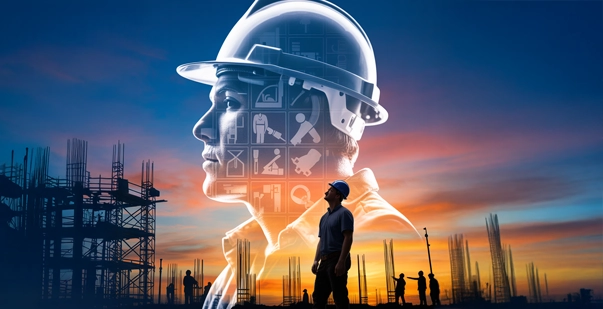
Stay safe and compliant during Construction Safety Week with top CE courses! Lea...
Read More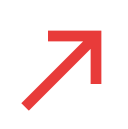
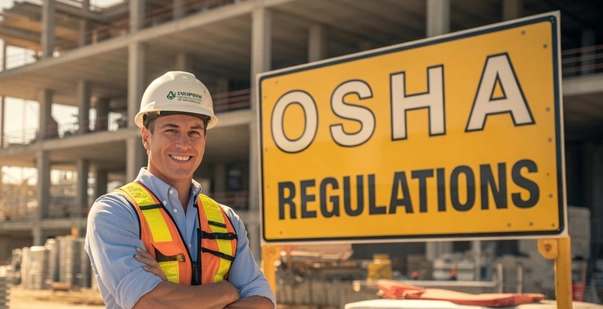
Stay compliant and protect your workforce — explore the latest OSHA heat regulat...
Read More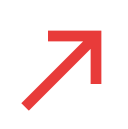
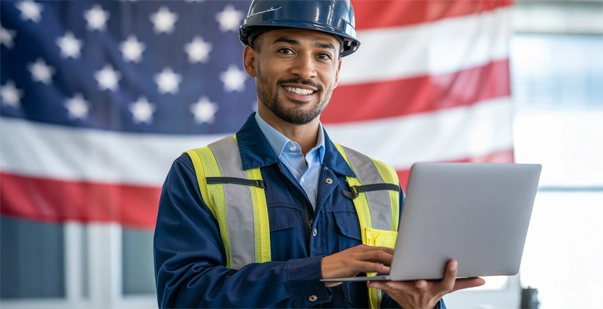
Celebrate freedom safely this 4th of July—get OSHA certified! Empower your caree...
Read More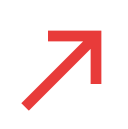
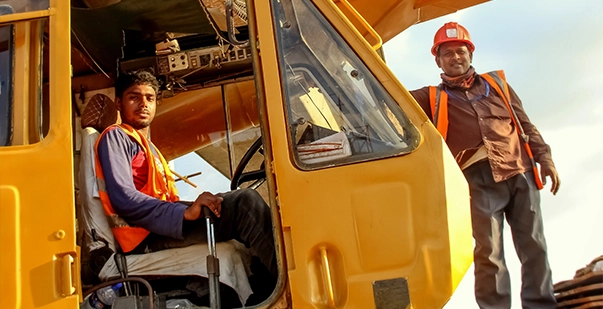
Dreaming of operating heavy machinery? Learn the steps to become a certified cra...
Read More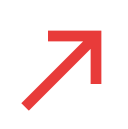
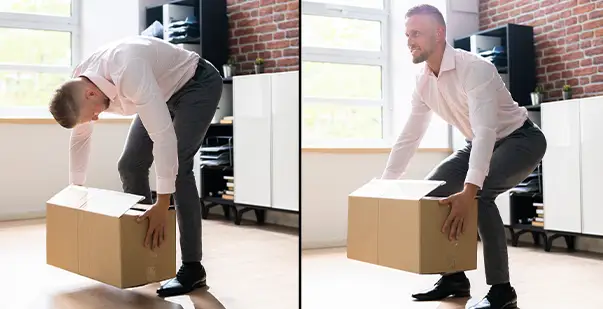
Protect your back and boost efficiency! Learn the ideal lifting technique—bend y...
Read More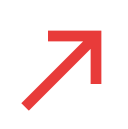
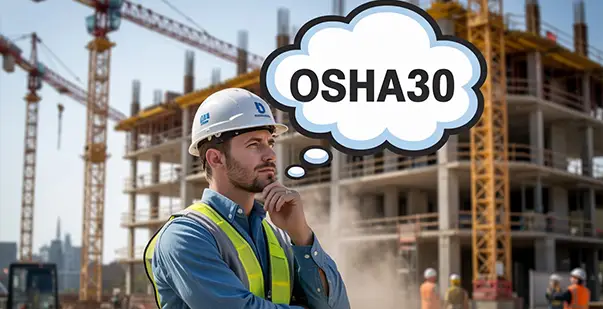
Wondering how long your OSHA 30 card stays valid? Learn about OSHA 30 expiration...
Read More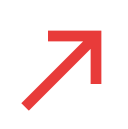
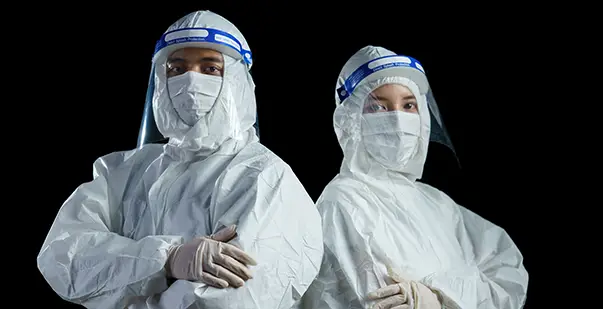
HAZMAT suits come in four levels—A, B, C, and D—each offering different protecti...
Read More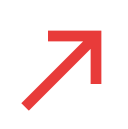
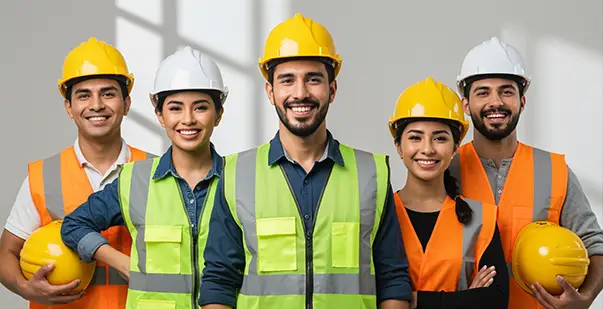
An SSHO, or Site Safety and Health Officer, ensures jobsite safety by enforcing...
Read More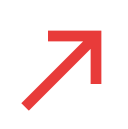
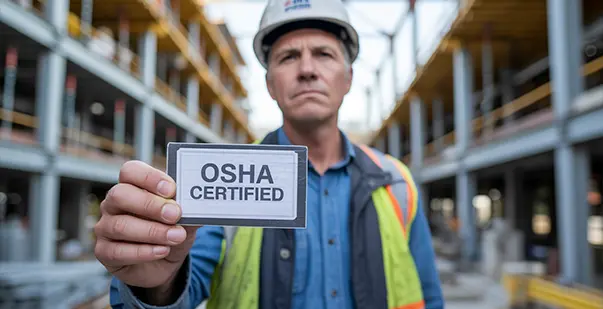
Lost your OSHA card? Don’t worry—replacing it is easier than you think. Follow o...
Read More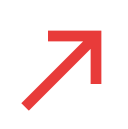
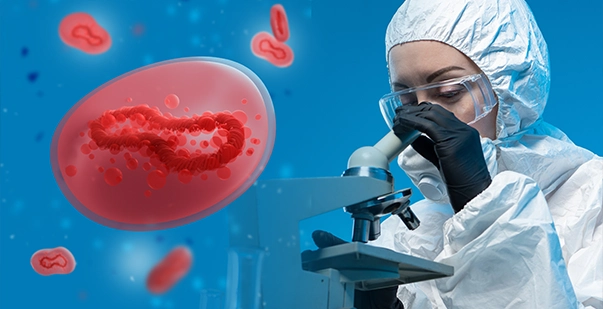
Learn what Bloodborne Pathogens Certification is, why it's crucial for workplace...
Read More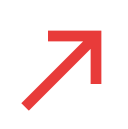
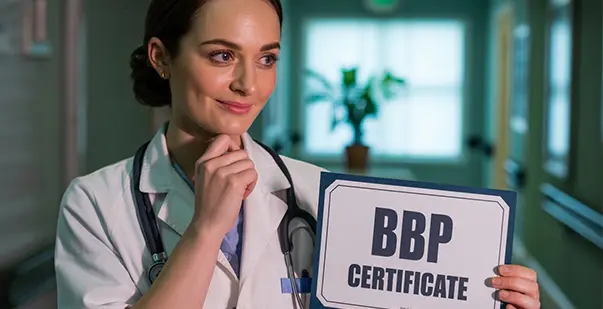
BBP certification typically lasts for one year. Stay compliant and safe by renew...
Read More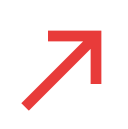
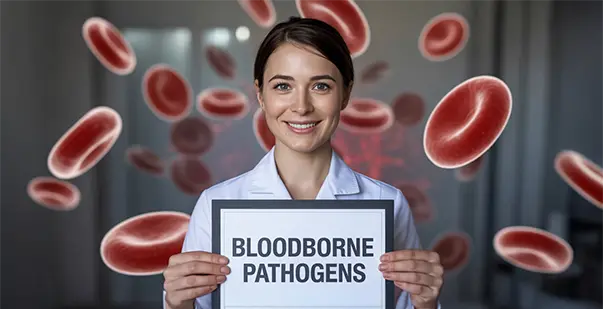
Stay compliant and safe in 2025! Discover everything you need to know about Bloo...
Read More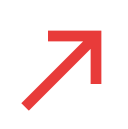
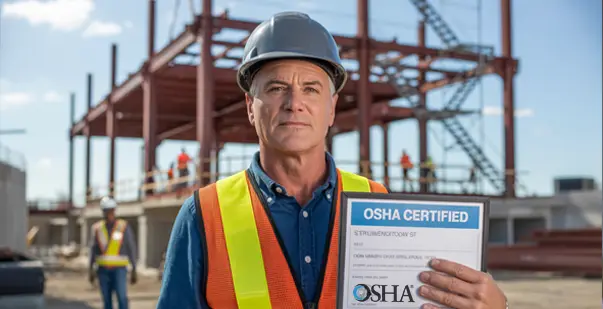
Wondering how many OSHA certifications exist? Discover the key types, from OSHA...
Read More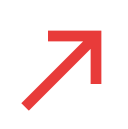
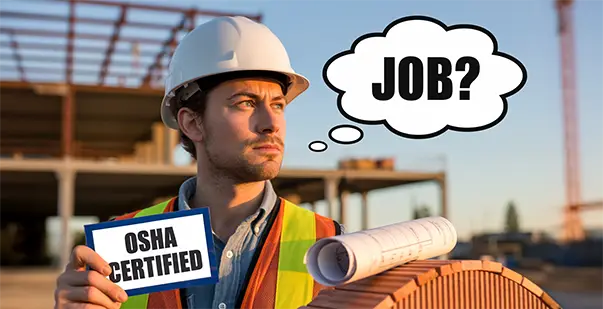
An OSHA card can open doors to jobs in construction, manufacturing, warehousing,...
Read More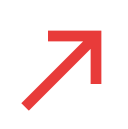
.webp)
NFPA 70E sets the standard for electrical safety in the workplace. Learn the key...
Read More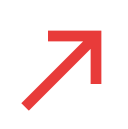
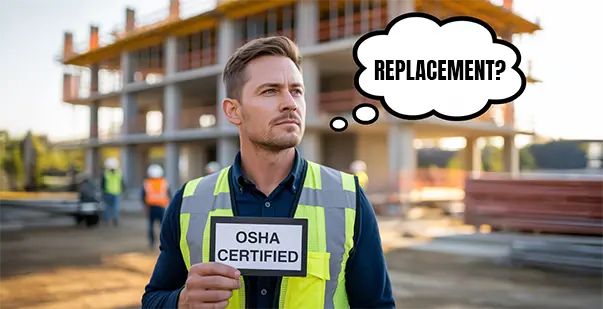
Lost your OSHA card? Don’t worry! Learn the simple steps to request a replacemen...
Read More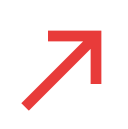
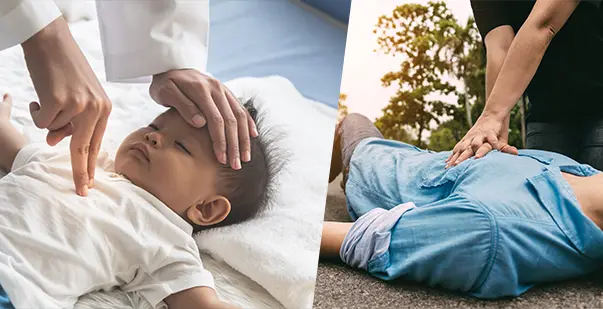
Learn the key differences between performing CPR on adults vs. children. From co...
Read More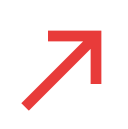
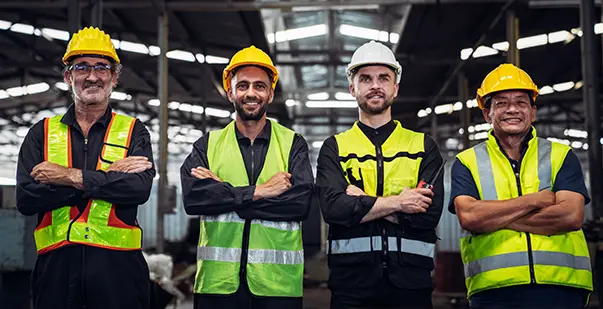
Celebrate Construction Appreciation Week by exploring how CE training empowers w...
Read More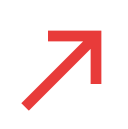
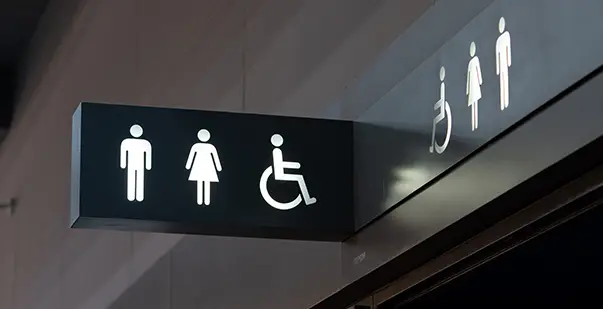
Learn what OSHA laws say about bathroom breaks in the workplace, employee rights...
Read More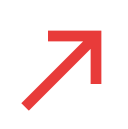
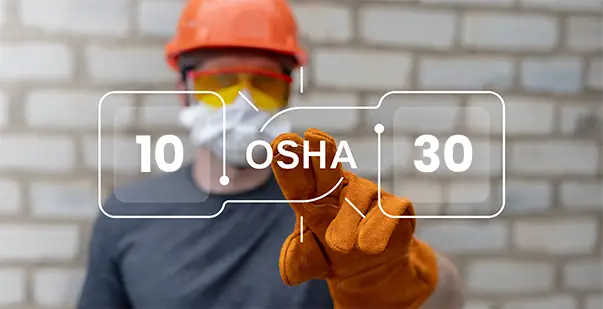
OSHA 10 and OSHA 30 differ in training depth, duration, and target audience. Lea...
Read More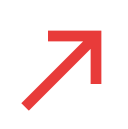
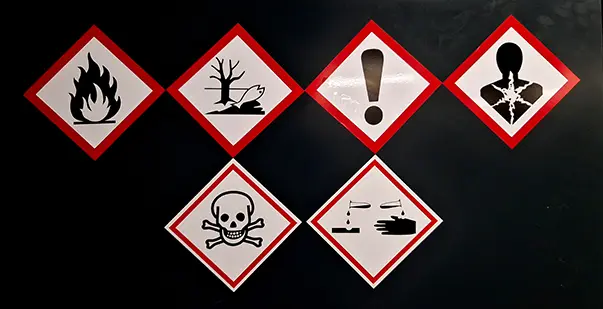
Learn the meanings behind GHS hazard signs, symbols, and pictograms to stay comp...
Read More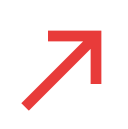